Electro Active Adhesive Layer.
Grab anything.
Reinventing the way robots and automated machines grab any object by unlocking unprecedented versatility, dexterity and energy efficiency,
on earth and in space
Reinventing the way robots and automated machines grab any object,
on earth and in space
Product
We produce electro-adhesive interfaces with tactile sensing feedback that can be easily mounted on any automatic machine or robot end effector. The product is based on the Electro Active Adhesive Layer (EAAL) implemented on a Conformable Back Structure, mounted as plug-&-play device on a Mounting Predisposition and powered by a standard 24V electronic unit.
The product is based on the Electro Active Adhesive Layer (EAAL), an electro-adhesive interfaces with tactile sensing feedback, implemented on a Conformable Back Structure, mounted as plug-&-play device on a Mounting Predisposition and powered by a standard 24V electronic unit.
For more info click here (1 min)
The advantages
Technology
The EAAL is a proprietary technology based on a flexible printed electronics thin-film that becomes adhesive on command through electrostatics on objects of all shapes and materials (such as dielectric or conductive, rigid or soft, dense or porous, planar or curve, solids or deformable, etc.), with an impressive force density, seamless conformability and sensor-AI feedback capabilities to detect proximity, contact, type of material or any valuable information from the gripping action.
The EAAL becomes adhesive on command through electrostatics on objects of all shapes and materials, with an impressive force density, seamless conformability and sensor-AI feedback capabilities to detect proximity, contact, or any valuable information from the gripping action.
Applications
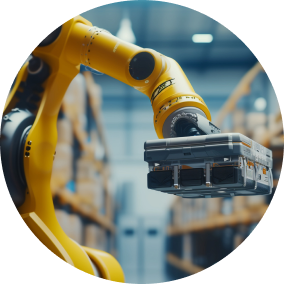
Industrial automation
packaging machines, adhesives applications, rollers, conveyor belts

Robotic grippers
pick&place, sorting
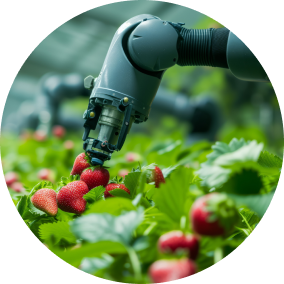
Agritech
fruits & vegetables, vertical, farming, gentle-handling
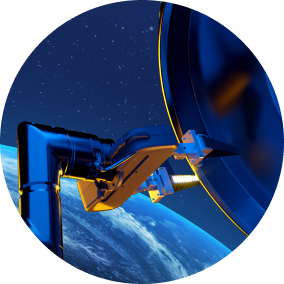
Space
docking, berthing, refuelling and maintenance to satellites, debris capture
No need for
Pneumatics
Heat dissipation
Magnets
Target predisposition
Press
Investors
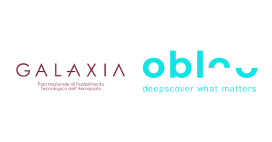
Honors and Awards
Find us
Legal headquarter: Via Filippo Turati 40, 20121, Milano
Operational Headquarter: Via Emilia Levante, 9/F, 40137 Bologna (BO), Italy
Space Headquarter: Corso Castelfidardo 30A, 10129, Torino (TO), Italy